Huntsville is famous for solving complex problems, but with a mixed bag of economic uncertainty and a workforce that is at times anxious and other times circumspect, finding solutions to North Alabama’s workforce challenges is ranking right up there with learning how to live long-term in outer space.
With the local unemployment rate at a record low 2 percent, it seems life would be all paychecks and rainbows. According to numbers recently released by the Huntsville-Madison County Chamber of Commerce, employment for most industry sectors in the metro have not only recovered but surpassed pre-COVID levels.
Moody’s is predicting growth in the Huntsville metro will double the pace of growth for the U.S. economy in five years.
At 2 percent unemployment, everyone should be working, production should be humming, and the biggest problem families should be facing is who is picking up the kids from school. Right?
Wrong.
The challenges ahead for workforce development in the three-county North Alabama region are very real and extremely pervasive.
The population in Madison County is growing rapidly, and workers are driving in from outside the metro to fill local jobs because there is a huge demand, and yet the labor supply is still very tight.
Alabama Industrial Development Training (AIDT) for North Alabama and the Robotic Technology Park (RTP) in Tanner are part of the state Dept. of Commerce. AIDT is part of a package given to companies receiving an abatement for being recruited to the state of Alabama. AIDT provides several services at no cost to the employer, including marketing for talent, help with the employee selection processes, onboarding employees, and job training to ensure companies find a qualified workforce.
Kristi Bain is assistant director of AIDT, and her organization has conducted several studies with employees based on job interviews and exit interviews to get a read on their mood.
Bain said they ask people outright, “Why are you turning down jobs?”
“Many females that were actively engaged before, have exited the workforce due to childcare,” said Bain. “But to complicate matters, many single parents are single parent males, and a flexible schedule is more important than money in these post-pandemic days.”
“The female population wants a different work environment, so we are actively offering them training in areas where they have never worked before like manufacturing,” she continued. “They want a steady shift where they know what their hours are going to be. That way they can remain an engaged parent like they got used to being during COVID.”
The solutions demand new and creative thinking and AIDT is working with companies to find creative avenues for job training to accommodate things like flexible schedules for childcare; to come up with some new incentives; and to find ways to create more flexible, or more consistent work schedules based on parent needs.
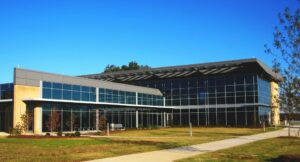
“In manufacturing and IT, things seem to be swinging back to normal, and people are coming back to work slowly,” Bain stressed. “Companies are hiring again rather than just back-filling attrition.”
AIDT works with new and expanding companies in manufacturing, logistics, IT, data centers and support areas in those industries.
They also have local partnerships with companies like the Alabama Institute for the Deaf and Blind (AIDB), and T&W Operations in Cummings Research Park.
They have an instructor that works with area high schools on base robotics and additive manufacturing, material-based 3D printing; AutoCAD; SOLIDWORKS, and CATIA.
Their 18-wheeler travels to schools and businesses throughout Madison County, staffed with three retired teachers in career technical areas from North Alabama.
“The truck can be programmed for kindergarten up to professional events so students or employees can engage and see different aspects of manufacturing in action,” she said.
It contains simulated forklifts with true controllers so they can engage with a collaborative robot, drones, a 3D printer and virtual welding onboard.
They also have a partnership with Operation Next, working with veterans as they take their next career step after military service.
“They can relocate anywhere in the U.S. and if they come to Alabama, we will do their training at no cost, so they don’t have to use their GI bill. They can save it to use it somewhere else with future training,” said Bain.
Other no cost training for people employed in Alabama include OSHA 10 safety classes, forklift, overhead crane, Lockout Tagout, and Arc Flash 70E Compliance.
On the robotics side, they train for Allen-Bradley and Siemans Programmable Logic Controllers (PLC), Omeron and Mitsubishi; FANUC, ABB digital and automation; Iscow computer and network technology; Motoman robotics; Kawasaki and KUKA. They offer hydraulics and pneumatics classes; basic electrical; Industry 4.0; vision machine and robotic paint training.
Visit https://www.aidt.edu/ to see a list of all the jobs they are working on with employers across the state.
Don’t miss out! Subscribe to our email newsletter to have all our smart stories delivered to your inbox.